While wheelbarrows are made from tough and durable materials, they are not indestructible.
They require proper maintenance and storage for optimal functionality.
However, due to space constraints, you might end up storing your wheelbarrow outdoors.
Proper oiling your wheelbarrow is an effective method of protecting it from the harsh winter and summer conditions.
This article will provide you with a comprehensive guide on maintaining your wheelbarrow.
Wheelbarrow Parts that Require Oiling
Wheel and Axle
Lubrication of the axle is essential for the smooth rolling of the wheelbarrow.
It reduces the friction between the axle and wheel as it rotates.
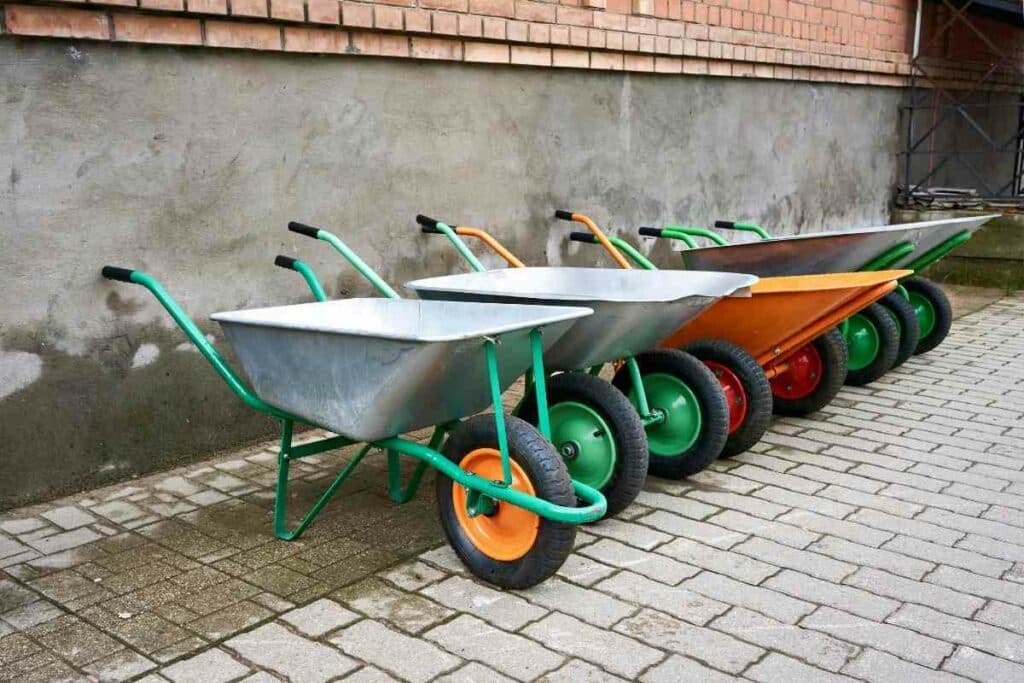
Moreover, you will expend less energy pushing your loads around the garden.
If your wheel has bearings, they will also need to be checked and lubricated when necessary.
Handle
Wheelbarrow handles tend to chip and have rough edges after prolonged usage.
Applying a layer of lubricants such as linseed oil can prevent the handles from chipping or rusting.
It will keep the handle in pristine condition and avoid unnecessary hand injuries from splinters and rusted protrusions.
Why Do You Need To Oil Your Wheelbarrow
Reduce Friction
Oiling your wheelbarrow reduces resistance to motion between the wheel and axle.
The film of oil between these parts enhances the efficiency and mobility of the wheelbarrow.
Prevent Corrosion
Over time, contaminants such as water or salts erode parts of the wheelbarrow.
A lubricant prevents corrosion by establishing a protective barrier between the contaminants and these parts.
It also slows down the rate of wear and tear.
Essential Properties of A Lubricant for Wheelbarrows
Viscosity
Viscosity refers to a lubricant’s resistance to flow and is determined by the oil’s molecular structure.
Low viscosity means a weaker molecular structure (London Dispersion forces) and thus less resistance to flow.
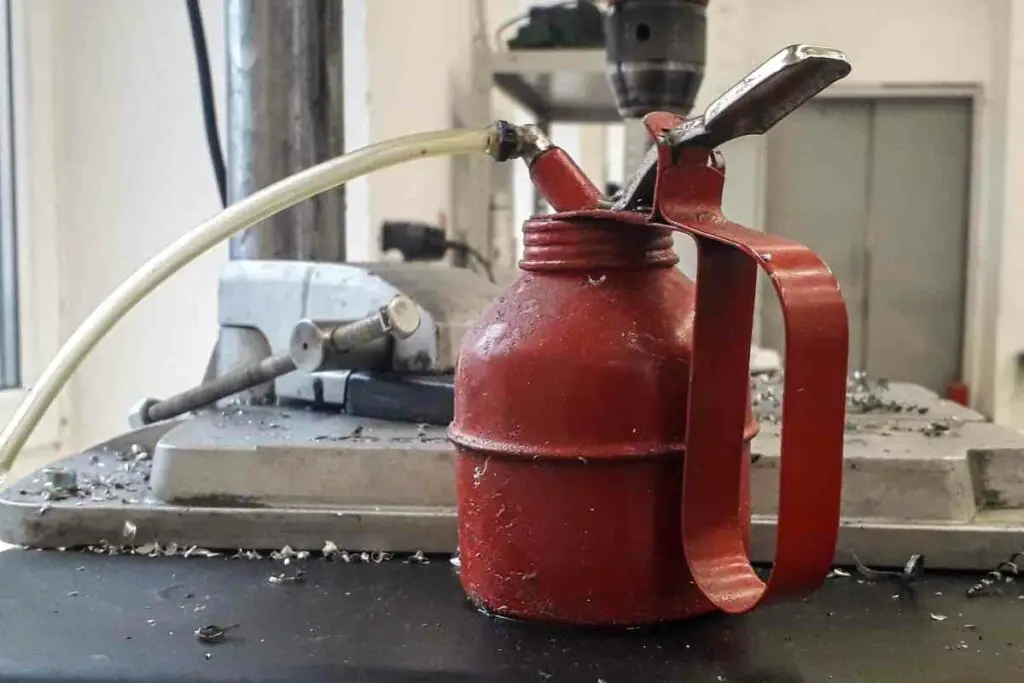
This is the best oil for wheelbarrows stored outside since easy dispersion and less friction make the wheelbarrow roll smoothly.
When heading into summer, look out for products with viscosity index improvers. As the temperature steadily increases, most mineral lubes will thin out.
These improvers expand with the increasing temperature to counteract the thinning of the oil.
Examples include:
- methacrylate polymers
- alkylated styrene
Pour Point
A pour point refers to the lowest temperature at which the lubricant will remain in its fluid state.
An oil with a low pour point or pour point depressants works optimally, especially during winter.
Under the freezing conditions, a high pour point will result in the oil crystallizing (solidifying) within the wheel system.
The clogged wheel will be unable to rotate rather than the oil facilitating smooth movement of your wheelbarrow.
Demulsibility
This is the ability of a lubricant to separate from water easily.
Water is the primary contaminant of oils and compromises its performance. Storing your wheelbarrow outside increases the probability of contamination.
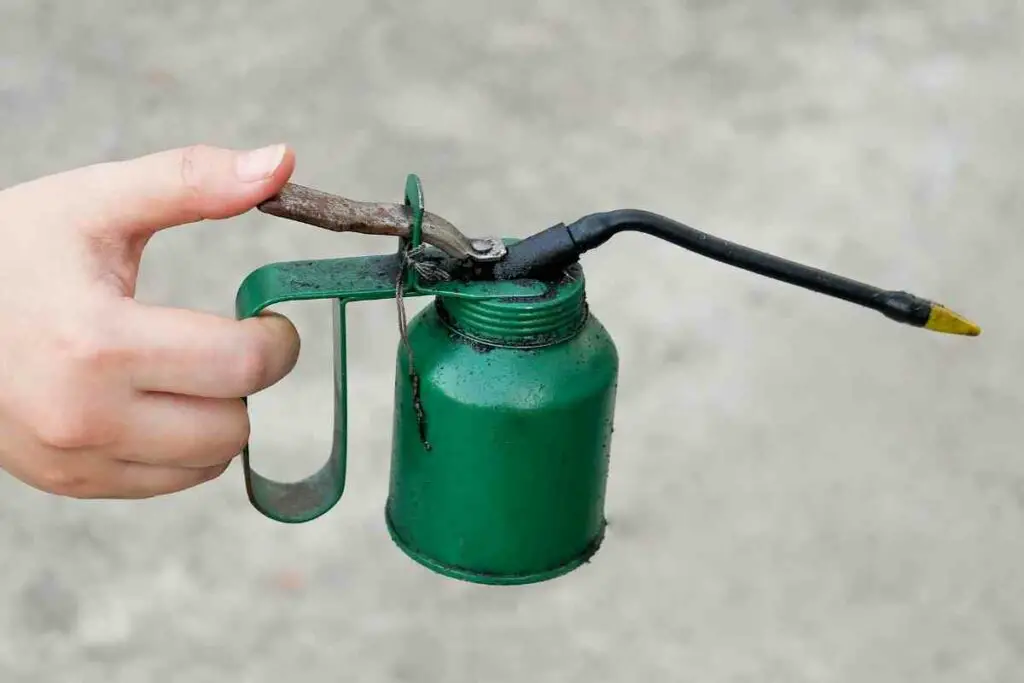
By virtue of water being denser than oil, it impedes the lubricant from forming a protective layer between the rotating parts.
As a Result – The friction in the wheel and axle increases. Consequently, this resistance will fasten the wearing of the wheelbarrow parts.
The degree of demulsification is determined by measuring its solubility properties.
For best performance, the optimum relative solubility number (RSN) should range from 8 to 15.
Products with an RSN higher than 17 usually are soluble in water and should be not used for wheelbarrows stored outside.
Oxidation Resistance
When a lubricant’s base oil is oxidized, it results in acidification.
This will ends up eroding the components of the wheelbarrow. It also leads to the formation of surface deposits that contaminate the oil.
The oxidation rate is low in winter but accelerates during the summer as it increases with an increase in temperature.
A high oxidation resistance will reduce the frequency of lubrication.
The oil will last longer, and you can do maintenance of your wheelbarrow quarterly without the parts getting damaged.
Non-Corrosive
Corrosion shortens the useful life of your wheelbarrow.

The presence of acidic properties in the oil is harmful, particularly to the metal surfaces of the wheelbarrow.
No water content should be present in the oil composition since it promotes corrosion.
Most new lubrication oils usually are weak alkalines or have a neutral ph. This protects against corrosion by neutralizing any acids and repelling off any contaminants.
Adhesiveness
This refers to the ability of a lubricant to attach to a surface firmly.
A good lubricant should spread evenly and adhere to the moving parts. The film of oil should not drip off from the surface during usage as well as storage.
Moreover, the oil should not stain the surface after drying.
If an adhesive additive is used, it must not interfere with the lubricant’s viscosity.
Often, additives thicken lubricants, increasing their viscosity. High density increases friction and reduces the efficiency of the wheelbarrow.
Temperature Range
A lubricant should have a high boiling point and a low freezing point.
The wide range in temperature points enables the oil to remain liquid for maximum functionality. This makes it possible to keep friction at a bare minimum.
A high boiling point means the lubricant won’t boil and evaporate, leaving the moving parts to grind upon each other.
On the Other Hand – A low freezing point prevents the thickening of the lubricant. This will actually increase friction between the wheel and axle.
Types of Lubricants
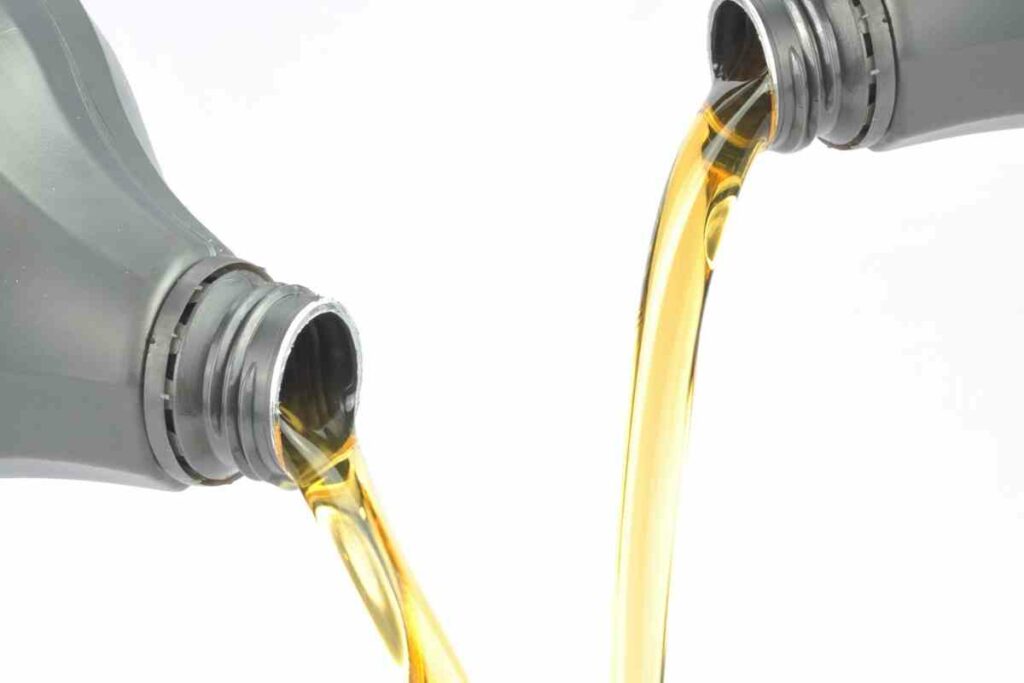
Oil
Oil is the most common form of lubricant.
It is relatively a thin liquid and may contain some additives.
These additives are synthetic polymers added to the base oil to increase efficiency.
Some of the common additives in wheelbarrow oil include:
- Antifreeze Agents: They ensure lubricating oils retain their liquid state at very low temperatures of up to −45°C. Examples are maleate-styrene copolymers and naphthalene waxes.
- Antioxidants: These slow down the Oxidation of the lube oil under high temperatures prolonging the intervals between oil changes. Examples include; aromatic amines and zinc dithiophosphates.
- Corrosion Inhibitors: They seek to prevent the corrosion of surfaces on exposure to corrosive agents such as water. Examples are fatty acids and alkaline-earth sulfonates/salts.
- Detergent Additives: Prevent the build-up of deposits on solid surfaces. They also neutralize any acid concentrates present in the oil, making it less effective. Examples include sulphonates and alkaline phosphonates.
Lubrication oils have different viscosities depending on the amount and type of additives used.
The more fluid your oil is (low viscosity), the less the fluid friction.
Consequently – There is low heat generation from the moving parts, and any heat build-up is quickly dissipated away.
Oil has a high boiling point and a low freezing point.
It is a reliable shield for wheelbarrows stored outside during extreme summer or winter temperatures.
The downside of using oil is it requires frequent lubrication since it’s not as adhesive as grease.
Grease
Grease is made by mixing mineral oil with thickeners.
The commonly used thickeners are lithium-based soaps.
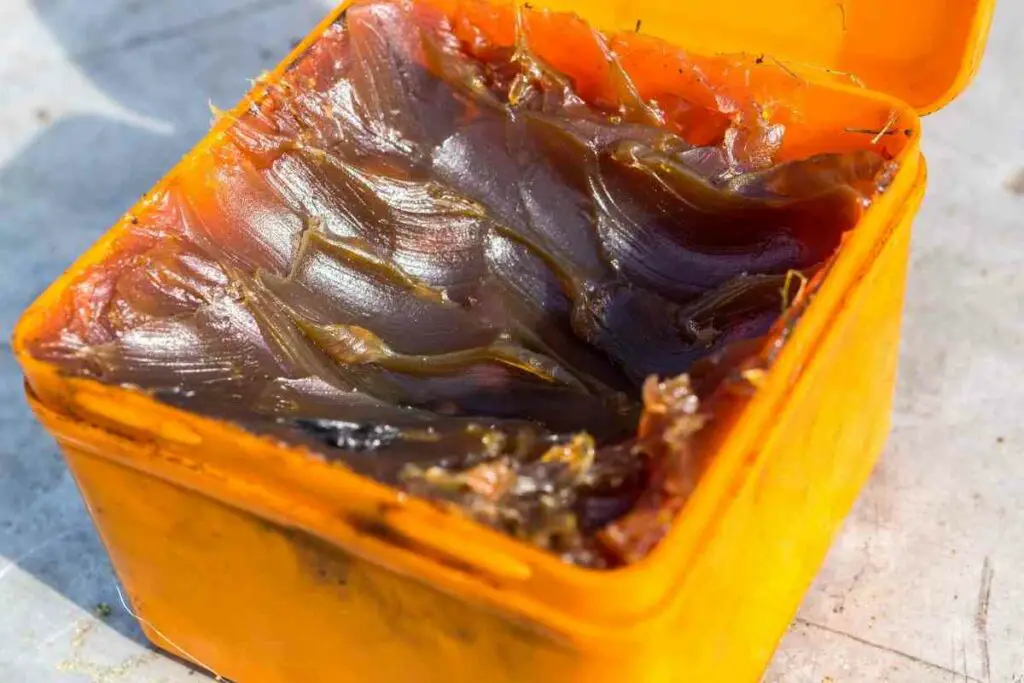
Additional lubricants such as PTFE, graphite, and molybdenum will often be added to the mixture to increase its viscosity.
Grease is denser than lube oil due to its texture and stickiness.
The properties help it adhere to surfaces better and for a much longer time. This will help protect your wheelbarrow surfaces from water and rust corrosion.
If you use your wheelbarrow seldom, grease is more suitable for you.
However, use lubricant with a low viscosity on the axles. Thick grease may create too much resistance hindering smooth movement as the wheel turns.
How To Test The Quality of Lubricants for Wheelbarrows
Manufacturers are required to carry out extensive quality tests during the production process of the lubricants.
The base oils, additives, and the final product are individually tested, and the data published for future reference.
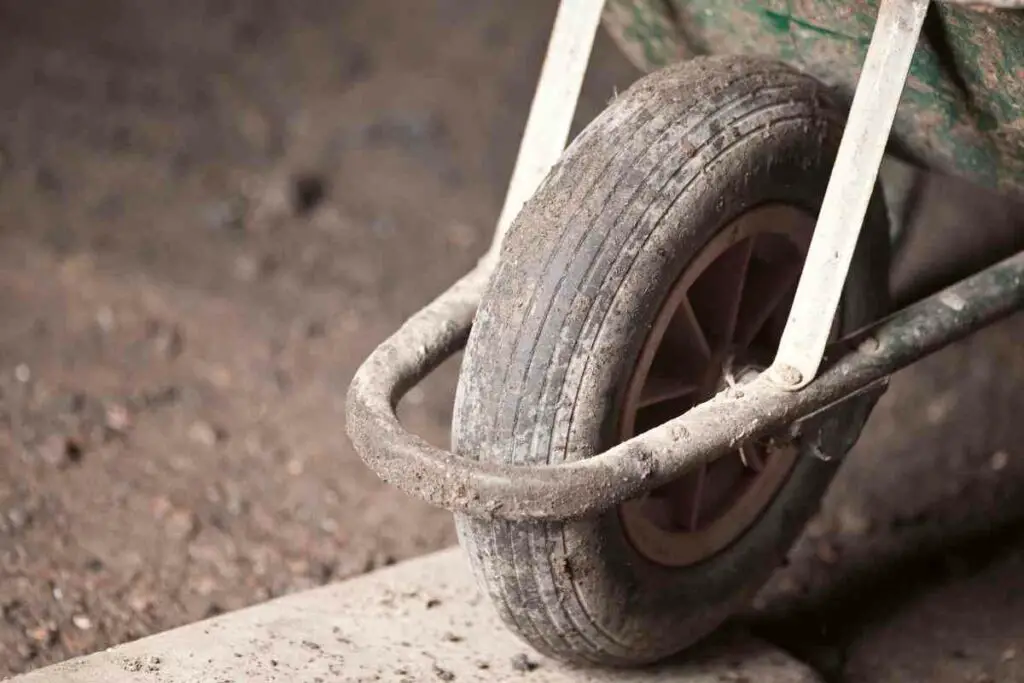
The ASTM International standards usually guide these company tests. It provides globally accepted guidelines to measure new lubrication products’ suitability and quality.
Moreover, they are used to monitor the performance of existing lubricants.
Some of the typical quality tests include:
- ASTM D1401 – Measure the oxidation stability of a lubricant
- ASTM D2896 – Identify and evaluate the base number of additives
- ASTM D665 – Determine the corrosion resistance of a lubricant
While most firms comply with the standards, false reporting is not uncommon.
This has led to the rise of private oil analysis laboratories.
The labs conduct independent tests to ascertain the effectiveness and the quality of particular products.
How To Oil A Wheelbarrow
Before applying lubrication to any wheelbarrow part, always ensure the surface is completely dry.
Oil floats in water; therefore, lube oil on a wet surface reduces its adhesiveness. It also makes the oil susceptible to being washed away.
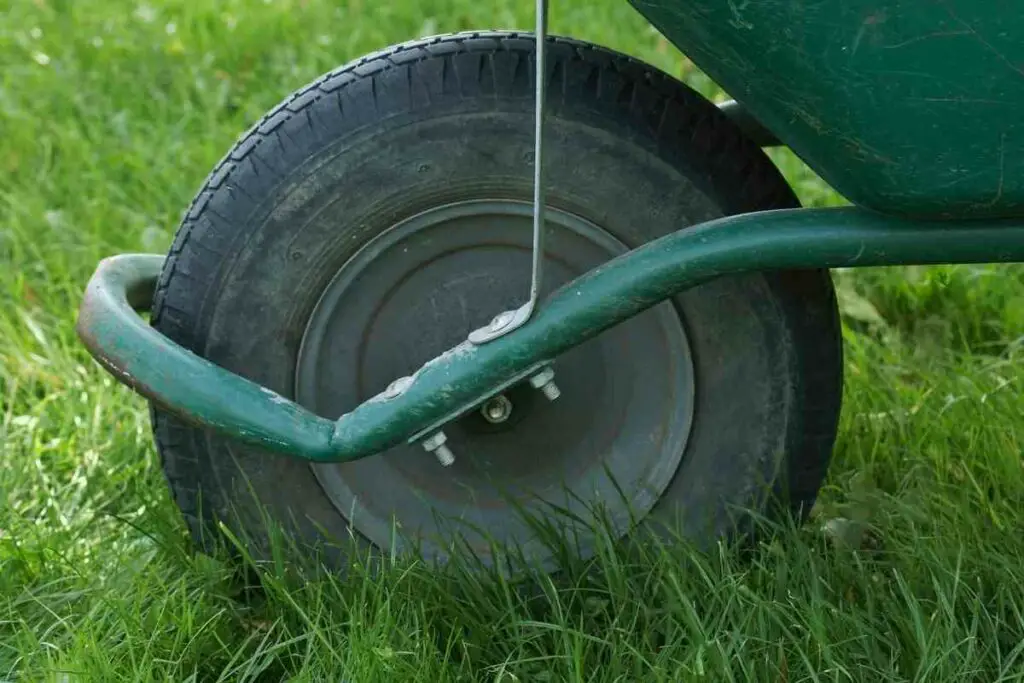
The surface should also be clean and free of solid particles such as dirt or mulch. Oiling a dirty surface increases the friction rather than reducing it.
The oil usually gums up with the solid particles forming a sludge, which hinders the lubricant’s effectiveness.
Apply the lubricant onto the contact surfaces using a grease gun or powering directly from the vessel.
Air it for a few minutes to allow the oil to dry off, and fumes dissipate before taking it into storage.
What Is The Best Oil For Wheelbarrows?
The lubricants to be used in the winter and summer seasons have to be compatible with most of the properties mentioned above.
However, all factors considered, the best oil for a wheelbarrow should be able to minimize friction and ensure the effective functioning of the wheelbarrow.
These are the core considerations when purchasing oil for your wheelbarrow.
Other factors such as the price, the brand, and the store your purchase from are down to your personal preferences.
Frequently Asked Questions
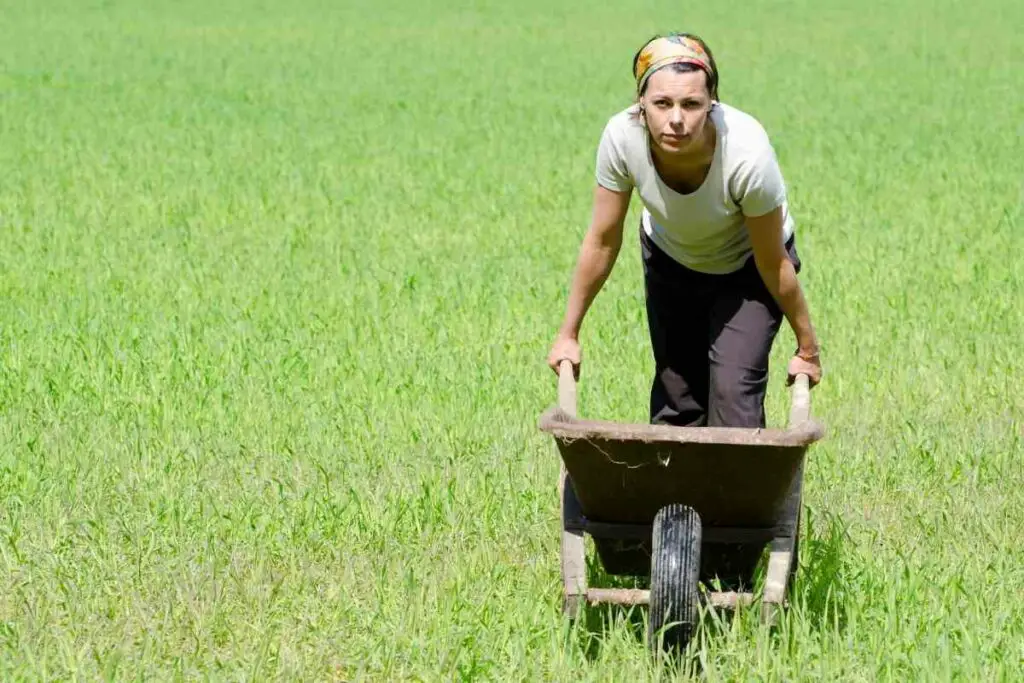
How Often Should You Lubricate The Wheel Axle?
This depends on how often you use the wheelbarrow and the storage duration.
Suppose you use it regularly and oil it once or twice a month, especially when it begins to squeak.
For occasional use and long periods in storage, we recommend after every 2 months to keep contaminants and corrosion at bay.
Can You Use Recycled Motor Oil to Lubricate The Wheelbarrow?
Recycled oil often contains impurities such as water, grit and acidic compounds.
While most of these impurities are relatively harmless, the acidic compounds are corrosive.
They attack the metal surfaces and ball bearings in wheels and hasten the wearing process.
The use of recycled motor oil is a common practice.
As much as it’s cheaper and gets the job done, it’s not as durable and effective as using fresh oil.
How Safe Are After-market Oil Additives?
While some supplemental lubricant additives are safe, it’s difficult to tell them apart with hundreds of products available.
Testing for compatibility and effectiveness is hectic and costly.
To avoid the need for these additives, we recommend you purchase quality broad-spectrum lubricants.
These lubricants contain all the requisite additives for efficient use and storage of wheelbarrows in summer and winter conditions.
Moreover, it’s cheaper to buy one premium product than to have an inferior lube that will require additional supplements.
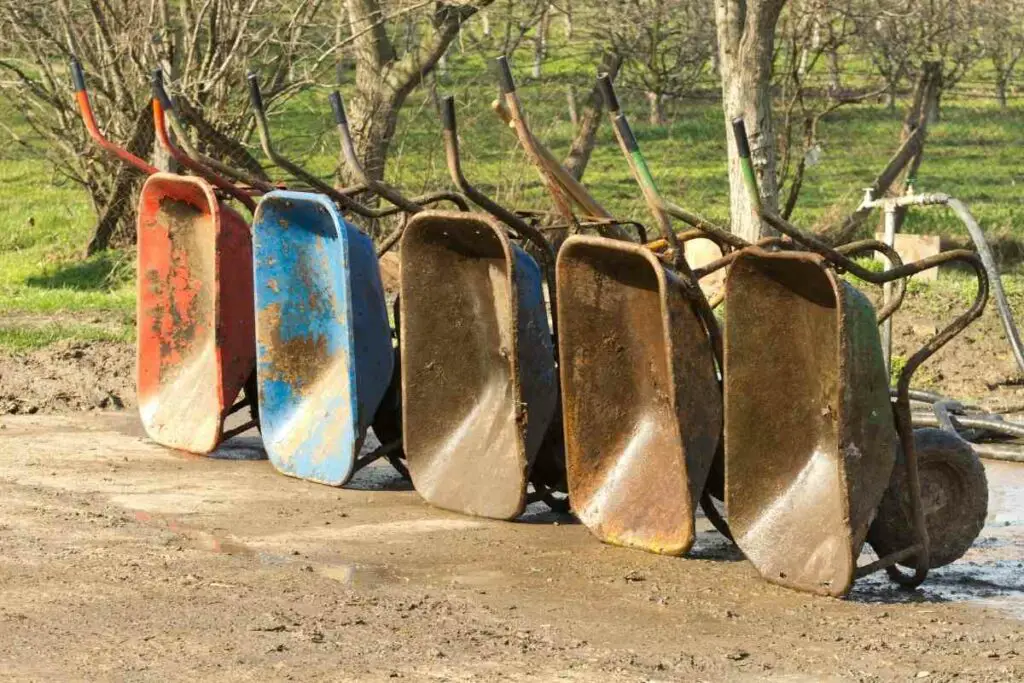
Does Lubricating Oil Freeze?
Typically, oil does not freeze since it lacks polarity.
This means that its molecules don’t have any positive or negative charge.
Besides, the hydrocarbon molecules vary in size, making it difficult to merge them.
Exposure to extremely low temperatures thickens as its chemical properties and additives deteriorate.
The viscosity, texture, and consistency are also affected.
Subsequently, the oil takes a long time to flow out of the storage container or the axle to rotate efficiently.
Final Words
While oiling comes in handy, your wheelbarrow is best stored in a shed or the garage.
Store it in a cool and dry area where it will be kept safe from corrosion by weather elements.
Prolonged exposure to these elements results in frequent repairs, high maintenance costs, and a significantly shorter useful life.
If you have to store the wheelbarrow outside, place it upright with the bucket tilted downwards.
This will prevent the accumulation of dust, debris, and precipitation. Consequently, you will significantly minimize rusting and corrosion.